NASTRAN Solution 146 MONPNT1 RMS in Aeroelastic Analysis
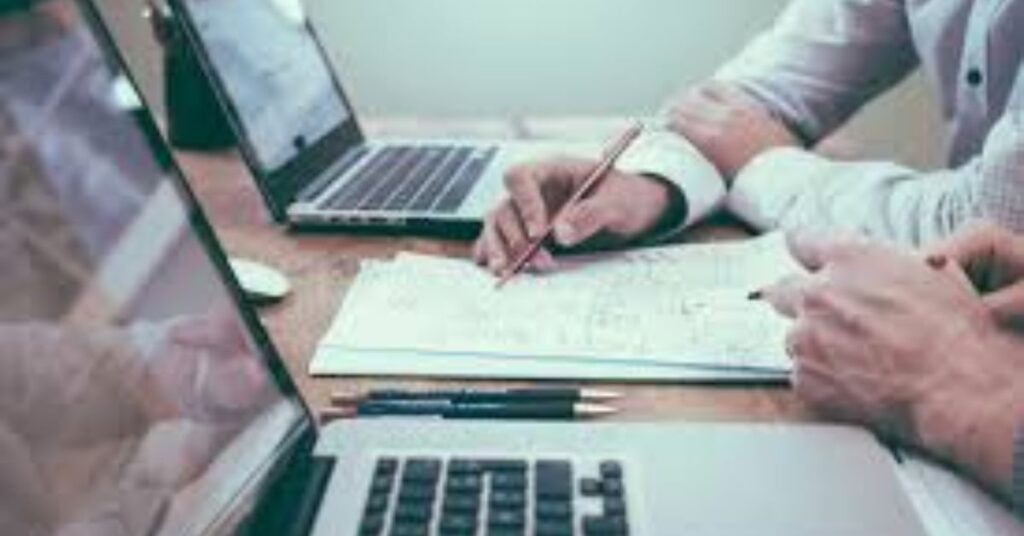
Introduction
In aerospace engineering, precision and reliability are essential when analyzing the complex interactions between aerodynamic forces and structural dynamics. NASTRAN Solution 146 MONPNT1 RMS, an advanced aeroelastic analysis tool, plays a critical role in helping engineers evaluate how aircraft structures respond to aerodynamic forces. Alongside it, key components such as MONPNT1 and RMS are crucial for tracking performance and ensuring accurate analysis.
In this article, we will explore NASTRAN Solution 146 MONPNT1 RMS, explaining their significance and how they are applied in the real world. We will cover key concepts, discuss the importance of these tools, and provide practical examples and solutions for common challenges.
1. What is NASTRAN Solution 146 MONPNT1 RMS?
NASTRAN Solution 146 MONPNT1 RMS is a specialized analysis solution within the NASTRAN software suite, designed for aeroelastic simulations. Aeroelasticity involves studying the interaction between an aircraft’s aerodynamic forces and its structural flexibility, which is critical for understanding the aircraft’s performance and safety under varying flight conditions. Solution 146 allows engineers to simulate phenomena such as flutter, aeroelastic response, and gust loads, which can lead to dangerous oscillations if not properly controlled.
This solution is widely used in the design and analysis phases to predict how an aircraft’s structure will behave under real-world aerodynamic conditions, helping engineers optimize structural integrity and flight performance.
2. Understanding MONPNT1
MONPNT1 is a monitoring point card used within NASTRAN to track specific aerodynamic forces, moments, and pressures during simulations. In the context of Solution 146, MONPNT1 plays a crucial role in outputting data from designated points on the aircraft model. These monitoring points provide insight into how aerodynamic forces, such as lift and drag, affect various sections of the aircraft.
For example, MONPNT1 may be used to track how much force is applied to the wingtips or fuselage under different flight conditions, providing engineers with vital information to refine designs and enhance performance.
3. What is RMS in Structural Analysis?
RMS (Root Mean Square) is a statistical measure used to quantify the magnitude of a varying quantity, often applied in the context of dynamic systems like vibrations, displacements, or stresses. In structural analysis, RMS helps engineers assess how structures respond to cyclical loads, such as those experienced during flight.
RMS values provide a clear indication of the average level of dynamic response over time, allowing engineers to evaluate the likelihood of fatigue or failure in aircraft components subjected to repeated stresses.
4. The Role of NASTRAN Solution 146 MONPNT1 RMS in Aeroelasticity
Aeroelasticity plays a critical role in aircraft safety and performance. As aircraft structures become lighter and more flexible, the risk of flutter and other aeroelastic instabilities increases. NASTRAN Solution 146 MONPNT1 RMS enables engineers to simulate and analyze these aeroelastic effects in a virtual environment, ensuring that aircraft designs can withstand aerodynamic forces without experiencing dangerous oscillations or deformations.
This solution allows engineers to assess the structural response under different flight conditions, including steady-state conditions and transient events like gusts. By accurately predicting these responses, engineers can prevent structural failures and improve overall flight safety.
5. Benefits of Using NASTRAN Solution 146 MONPNT1 RMS
The benefits of using NASTRAN Solution 146 MONPNT1 RMS in aerospace engineering include:
- Accurate flutter prediction: Helps engineers identify flutter conditions and adjust designs to avoid dangerous oscillations.
- Improved safety: By simulating real-world aerodynamic forces, engineers can ensure that the aircraft structure remains stable under various flight conditions.
- Optimized design: Solution 146 enables engineers to fine-tune structural elements, such as wings and fuselage, to improve aerodynamics and reduce weight without sacrificing performance.
- Cost efficiency: By identifying potential issues in the design phase, engineers can avoid costly revisions during physical testing or later in production.
These benefits underscore the importance of NASTRAN Solution 146 MONPNT1 RMS in ensuring the safety and efficiency of modern aircraft designs.
6. How MONPNT1 Enhances Simulation Accuracy
MONPNT1 is essential for providing accurate data on aerodynamic forces and moments during simulations. By setting up multiple monitoring points across key areas of the aircraft, engineers can track how aerodynamic forces change across different sections. This level of detail allows for more precise simulations and helps engineers identify areas where the design may need adjustments.
Without accurate monitoring points like MONPNT1, engineers would be unable to capture critical data, leading to less reliable simulations and potentially flawed designs.
7. RMS in Finite Element Analysis
In finite element analysis (FEA), RMS is used to calculate the magnitude of dynamic responses such as vibration or displacement. RMS values are particularly important when analyzing the fatigue life of aircraft components, as they provide a measure of how much stress or strain the structure experiences over time.
By calculating RMS values, engineers can assess whether a structure will remain reliable under repeated loading conditions, ensuring that components are designed to withstand the demands of flight.
8. Real-World Applications of NASTRAN Solution 146
NASTRAN Solution 146 has been applied in a wide range of real-world scenarios, particularly in the aerospace industry. Some common applications include:
- Aircraft wing design: Solution 146 is used to simulate aeroelastic behavior and optimize wing shapes to prevent flutter and improve fuel efficiency.
- Spacecraft structures: Engineers use the solution to ensure that spacecraft can handle the extreme aerodynamic forces experienced during launch and re-entry.
- Unmanned aerial vehicles (UAVs): For UAVs, Solution 146 helps optimize lightweight structures for stability and performance under varying flight conditions.
These applications demonstrate the versatility and importance of Solution 146 in modern aerospace engineering.
9. Common Challenges in Using NASTRAN Solution 146
While NASTRAN Solution 146 offers significant advantages, there are some challenges engineers may encounter:
- Complex setup: Configuring the simulation model for aeroelastic analysis can be time-consuming, especially when setting up monitoring points like MONPNT1.
- Computational demands: Aeroelastic simulations require significant computational resources, which can result in long processing times.
- Accuracy of input data: The accuracy of the simulation depends heavily on the precision of the input data, including material properties, aerodynamic loads, and structural configurations.
Understanding these challenges is essential for achieving reliable results in aeroelastic simulations.
10. Overcoming MONPNT1 Configuration Issues
Setting up MONPNT1 monitoring points can be tricky, particularly in complex structures with many components. Some common issues include misplacing monitoring points or setting incorrect parameters, which can lead to inaccurate data collection. To overcome these challenges, engineers should:
- Validate monitoring points: Ensure that the points are correctly placed at critical locations.
- Double-check parameters: Verify that the settings for each MONPNT1 card are accurate and reflect the desired outputs.
- Run smaller test simulations: Before running a full simulation, perform smaller tests to verify that the monitoring points are functioning as expected.
By following these best practices, engineers can avoid common pitfalls and ensure accurate data collection.
11. How to Calculate RMS in Structural Analysis
Calculating RMS in structural analysis involves several key steps:
- Collect dynamic response data: Gather data on the displacement, stress, or strain values over time.
- Square each value: Squaring eliminates negative numbers and focuses on the magnitude of the response.
- Find the mean of the squared values: Take the average of all the squared values.
- Calculate the square root: Finally, take the square root of the mean to get the RMS value.
This method provides a clear measure of how much stress or strain a structure experiences during cyclic loading.
12. Case Studies: NASTRAN Solution 146 in Action
Case Study 1: Reducing Flutter in a Military Aircraft
In the design of a new military aircraft, engineers used NASTRAN Solution 146 to identify potential flutter issues during high-speed maneuvers. By placing MONPNT1 points at key locations along the wings, they tracked aerodynamic forces and optimized the wing design to reduce flutter risk.
Case Study 2: Optimizing a Commercial Airliner’s Wing Design
A major aircraft manufacturer used Solution 146 to optimize the aeroelastic performance of a commercial airliner’s wings. By analyzing RMS values, the engineers were able to predict areas of potential fatigue and adjust the design to extend the aircraft’s service life.
These case studies highlight the practical applications of Solution 146 in aerospace engineering.
13. Future of NASTRAN in Aerospace Engineering
As computational power increases and simulation technologies evolve, NASTRAN is expected to play an even greater role in aerospace engineering. Future developments may include:
- Faster simulations: With improved computational capabilities, simulations will become faster, allowing for quicker design iterations.
- Integration with AI: AI may be used to optimize simulations and provide more accurate predictions in less time.
- Advanced materials: As new materials are developed, NASTRAN will continue to be an essential tool for evaluating their performance under real-world conditions.
These trends point to a bright future for NASTRAN in the field of aerospace design and analysis.
14. Conclusion
NASTRAN Solution 146, along with MONPNT1 and RMS, provides engineers with the tools needed to accurately simulate and analyze aeroelastic effects. From predicting flutter to optimizing structural performance, these tools play a critical role in ensuring the safety and efficiency of modern aircraft designs. As technology advances, these tools will continue to evolve, offering even more precise simulations and faster design processes.
For engineers looking to enhance their aeroelastic simulations, NASTRAN Solution 146 is an indispensable asset that leads to safer, more efficient aircraft designs.
FAQs
1. What is the primary purpose of NASTRAN Solution 146 MONPNT1 RMS?
NASTRAN Solution 146 MONPNT1 RMS is used for aeroelastic analysis. Allowing engineers to simulate the interaction between aerodynamic forces and structural flexibility.
2. How does MONPNT1 improve simulation accuracy?
MONPNT1 provides precise data on aerodynamic forces at specific points, helping engineers make informed design decisions.
3. Why is RMS important in structural analysis?
RMS helps measure the dynamic response of a structure, such as vibrations. Which is crucial for predicting fatigue and structural performance.
4. What are some challenges in using NASTRAN Solution 146 MONPNT1 RMS?
Challenges include complex setup, high computational demands, and the need for accurate input data.
5. How is NASTRAN Solution 146 MONPNT1 RMS used in real-world applications?
NASTRAN Solution 146 MONPNT1 RMS is used in various aerospace applications, from reducing flutter in military aircraft to optimizing wing designs for commercial airliners.